Perfilado: es más fácil ganar a la lotería que encontrar un técnico especializado
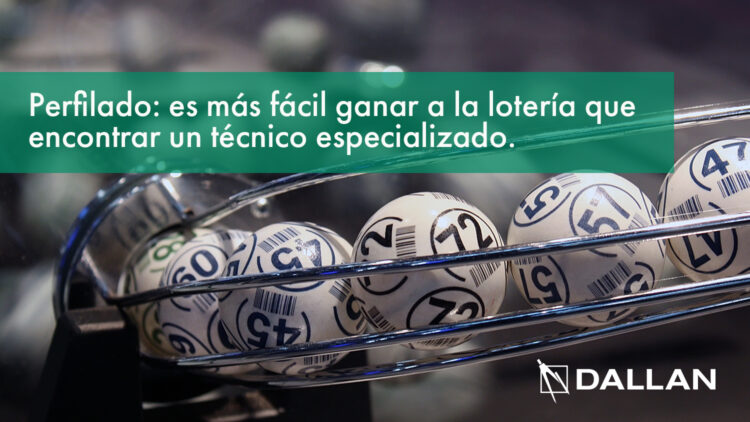
La dificultad de encontrar personal productivo, especialmente en Europa y Norteamérica, se ha convertido en un problema cada vez más extendido.
Esto va acompañado de la voluntad de limitar lo máximo posible los costes de producción, sustituyendo al personal destinado a operaciones simples o repetitivas por sistemas automatizados. El sueño prohibido de los empresarios y de las empresas es llegar a producir con un número mínimo de empleados o con ninguno.
Por tanto, me encontraba frente a una doble exigencia.
Por un lado, veía la voluntad de las empresas de adquirir líneas muy automatizadas que permitían partir de la materia prima bruta y llegar, si era posible, al producto embalado y preparado para ser enviado, utilizando el mínimo de personal. Esto precisaba líneas que ofrecieran un gran nivel de sofisticación.
Por el otro, era necesario proponer líneas que fueran muy fáciles de usar. En efecto, cada vez resultaba más difícil encontrar personal cualificado y las empresas no querían comprometerse con técnicos excesivamente especializados, que eran los únicos que conocían el “secreto” de la perfiladora que tenían a su cargo.
Las automatizaciones y las máquinas tenían que ser fáciles de usar por personal no especializado.
Extraído del libro «La Revolución de la Eficiencia»
SOLICITE EL LIBRO GRATIS
Hemos visto en el capítulo anterior que las automatizaciones Coil To Pack supusieron un gran éxito a la hora de aumentar la productividad de las líneas para perfiles de cartón-yeso.
Yo también lo pude constatar en las líneas de fabricación de perfiles para falso techo FTD (T-bar). Esta era otra de las grandes especializaciones de la empresa. El T-bar es un perfil en forma de T invertida, compuesto por un cuerpo de chapa galvanizada y un revestimiento de chapa o aluminio prelacado.
Para la producción de estos perfiles, un cliente alemán quería activar una serie de líneas de producción de muy alta capacidad. Para este proyecto, las líneas tenían que producir el doble de perfiles que las máquinas que ya había en el mercado en ese momento, con solo un cuarto del personal.
El análisis reflejó que había que tener en cuenta no solo la producción del perfil, sino también la secuencia de control de calidad y el embalaje del producto. Consideramos la línea bajo múltiples aspectos: tamaño y longitud de las bobinas, velocidad de producción, tasa de consumo de los materiales dentro de la perfiladora, calidad de las materias primas, tipo de embalaje que hay que realizar, estudio ergonómico del peso de los paquetes de perfiles y conexión con el sistema de visión para controlar la calidad de los perfiles.
Como resultado, surgieron las primeras líneas completamente integradas Coil To Box, a partir de bobina al perfil acabado en la caja, ya colocado en el palé para flejar y enviar.
Los sistemas producían estos perfiles estéticos, muy técnicos y complejos, a una velocidad de más de 100 metros por minuto.
Para hacer todo ese trabajo, necesitábamos solo tres supervisores por cada dos líneas, principalmente para asegurar el suministro de materia prima en las máquinas, que–literalmente– consumían toneladas y toneladas de chapa galvanizada, prelacada, acero de alta resistencia para los clips, cajas de cartón para el embalaje y cola. Al final de la perfiladora, las cajas de cartón estaban perfectamente ordenadas y apiladas en los palés listas para entregar.
También los sistemas Coil To Window, que ya vimos en el caso de Profalux y del grupo Stella, son excelentes para introducir la automatización en la producción de persianas. En este caso, aunque se trata de automatización, no hablamos de embalaje, sino de fabricación.
Los sistemas Coil To Window también se utilizan para otro tipo de productos relacionados con la protección solar: las lamas venecianas de exterior.
Hasta hace unos años, estos productos eran especialmente demandados por el mercado suizo, austriaco y alemán. En la actualidad, la demanda se ha extendido a toda Europa del Este y Francia, y está empezando a llegar a Italia. Las lamas venecianas de exterior, en comparación con las persianas enrollables, presentan la ventaja de permitir la modulación de la luz dentro de la estancia, variando la inclinación de las lamas.
Igual que en el caso de las persianas enrollables, al ser todas las ventanas diferentes, las persianas metálicas pueden ser también diferentes entre sí. Es absolutamente indispensable poder gestionar la producción sin tener que programar las máquinas de forma manual.
Hay dos tipos principales de sistemas de venecianas: el sistema en C y en Z. Al contrario que las persianas, estos estores cuentan con sistemas de fijación más complejos, que necesitan la aplicación de pasadores y fijaciones en los extremos de los perfiles y el montaje en escalerillas de formas diferentes.
Hasta el 2005, las máquinas perfiladoras realizaban exclusivamente los perfiles que después se fijaban a mano en chasis apropiados. El montaje era siempre la operación más larga y no la producción de perfiles, que se podían fabricar a una velocidad de sesenta metros por minuto.
Dallan siempre ha estado presente en este mercado, que concierne a los perfiles de chapa fina y prelacada, por tanto, era una de nuestras especializaciones. Nuestros clientes empezaron a pedir sistemas para realizar el montaje de los perfiles en las plataformas. Por eso, empezamos a estudiar y a diseñar los primeros sistemas de aplicación de fijaciones y los primeros sistemas de inserción, que acabamos patentando.
Es tanta la cantidad de trabajo que se demanda para el montaje manual de estos perfiles, que las automatizaciones acaban pagándose en muy poco tiempo.
Los sistemas Dallan para lamas venecianas se diseñaron con la misma lógica del sistema de persianas. Diferentes estaciones de trabajo y montaje separadas que hacen de buffer para equilibrar el tiempo de trabajo de todas las estaciones. Con el tiempo, hemos tratado de equilibrar la velocidad de las diferentes máquinas para no tener cuellos de botella durante el proceso lo que nos ha permitido crear extraordinarias aplicaciones.
¿El resultado? En este vídeo, se puede ver un sistema como el de las lamas venecianas en C:
La primera parte de la perfiladora produce los perfiles preparados para las perforaciones. El perfil transformado y cortado se entrega a un grupo de transportadores y se lleva a la máquina que aplica los pasadores. A través de una segunda serie de transportadores, los perfiles llegan a la última estación de montaje, donde se introducen uno a uno en la escalerilla.
La persiana metálica montada es extraída por un operador o manualmente y, por lo general, se deposita en carritos especiales para ir a las estaciones finales de ensamblaje.
En estas estaciones, la persiana metálica se abre, se controla y se añaden los últimos accesorios: el perfil extrusionado en la base, que equilibra el peso y la tensión de la persiana, se añaden las correas de elevación y la motorización, que se introduce en el perfil de cabezal en C.
Gracias a estas soluciones, los perfiles se realizan y se montan reduciendo al mínimo el trabajo manual y los almacenamientos intermedios que permiten un cambio muy rápido del perfil y del color de la cinta.
También hay un sistema perfectamente similar para los perfiles en Z, que necesitan un montaje aún más complejo. En efecto, en estos perfiles se instalan fijaciones laterales que se cierran en escalerillas específicas. También en este caso tuvimos que diseñar un sistema de estaciones de trabajo independientes que permitiera simplificar el montaje y llegar en muy poco tiempo de la bobina a la persiana acabada y lista para el montaje final.
Estas automatizaciones redujeron a menos de un tercio el personal necesario para el trabajo de tipo tradicional, introduciendo otras importantes ventajas, como la reducción del work in progress y la introducción de sistemas de gestión de la producción centralizados, gracias a la programación paramétrica que permite cargar los datos del pedido directamente del ERP de la empresa.
La ilustración muestra que el programa integrado en la máquina también permite que el operador compruebe la forma de una persiana metálica antes de mandarle la orden de producción a la máquina.
El programa de gestión de estas líneas es un valor esencial para la empresa. Los últimos sistemas permiten controlar los pedidos en producción, enviar listas de trabajo y recibir feedbacks automáticos sobre la producción ya realizada, además de gestionar la producción de chapas adicionales en vista de posibles reparaciones, cuando aparecieran problemas en las operaciones manuales de montaje de refuerzo.
Con la fusión del 2013, incorporamos a Dallan la empresa Elda, especializada en la producción de cuadros eléctricos y programas para las líneas Dallan. Al tener dentro de la empresa al equipo de informáticos que había creado el programa de gestión, pudimos responder de manera puntual a las exigencias del mercado, gracias a programas que ofrecen soluciones que superan con mucho las expectativas los clientes.
Hoy día, el equipo informático interno es una ventaja esencial que permite aportar a nuestros clientes un valor añadido, gracias a la automatización de partes importantes del flujo informativo de la empresa.
¡En efecto, como hemos visto, la filosofía LEAN recomienda no solo eliminar los residuos de material, sino también el flujo de información y los procesos en papel que no producen ningún valor añadido para el cliente!
Gracias a la flexibilidad aportada por un equipo de desarrolladores de programas, se pueden proponer soluciones como la que se presenta a continuación:
En ese caso, el flujo de información se optimizó y, aunque dejamos un margen de acción al responsable de producción y al operador, eliminamos todo el flujo de pedidos en papel y la inserción manual de la información, con los errores que esto puede traer consigo.
Extraído del libro «La Revolución de la Eficiencia»
SOLICITE EL LIBRO GRATIS
Andrea Dallan
CEO – Dallan Spa