Drywall Profiles: The Basics
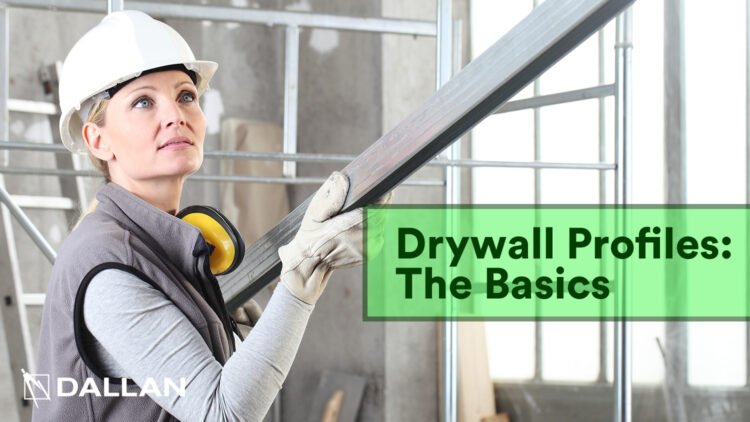
The drywall system has a very long history: in fact, the very first plant for producing construction panels for dry construction was built in England in 1888.
It was an alternative to wooden panels, and the product quickly became successful thanks to its fire resistance properties and, later, thanks to the technical water-resistant panels that are available on the market today and that can be used not only for interior walls but also for exterior walls.
In dry construction, the panels are applied to the underlying structure, which was originally made of wooden beams.
The support frame required horizontal and vertical elements, called studs, which had to be placed at regular distances to allow the panel to be fixed.
Wooden structures are still present in some markets, but they have been progressively replaced by metal profiles that have much better strength and versatility, also for their fire resistance.
Profiles can have different sizes according to the standards of different countries and markets.
The most well-known are, for example, the American, German, and French standards.
In all these standards, the profiles have a thickness between 0.4 and 0.7mm.
There are hundreds of different profiles, including finishing profiles like perforated corner beads.
Here we will see the most common ones, i.e., the stud and track profiles used for the construction of interior walls, and ceiling profiles.
In fact, the drywall system is used to efficiently and quickly also create special ceilings, which include lighting points, ventilation systems, and so on.
For walls, the tracks are positioned at the floor and ceiling level, and have the shape of “U” profiles.
The studs are positioned vertically inside the tracks, at the distance at which the panel edges will be positioned.
In the studs, there are normally a series of round, oval, or “H” holes for the passage of cables and pipes.
The panels are then fixed with special self-tapping screws, and the space between the panels is often filled with insulating materials like rock wool.
The size of guide and stud profiles in Europe ranges from 50 to 150mm.
For ceilings, the profiles have a C shape and are called CD profiles, or Fourroure for French-speaking markets. They are fixed to the ceiling with special accessories, then the panels are fixed to the profiles with the same self-tapping screws.
Aside from these main profiles, there are hundreds of different profiles that are used for finishing: flexible tracks, perforated corner beads with different shapes, plastering profiles (T profiles), and so on.
For all these other profiles, there are specific production systems, but the beauty of the drywall system is that all the profiles can be made with a very limited number of machines!
Even though this is considered a mature market, there are continually innovations made to the profiles. One of these is the profiles with an embossed surface, which we call XST.
This surface improves the grip of the screws to the profile, and improves the overall rigidity of the profile, compared to profiles with the same base material.
This processing can be inserted into each existing production system.
Turning to production systems, the typical set of profiles to start production is the following:
- 3 guide profiles
- 3 stud profiles
- 1 ceiling profile types CD or Fourroure
- 1 guide for ceiling profiles type UD or angle
These profiles allow to produce and sell all the main components required in the different markets and to start with a complete profile system for drywall!
As a company, you can have different needs.
A start-up, for example, makes profiles for its own use and in this case, a system that produces at 30 or 60 meters per minute is sufficient.
In this case, the D4V system produces at 60 meters per minute and allows to produce, under normal conditions, up to 20,000 meters of profile in an 8-hour shift – considering coil changes and product changes.
Here you can see a video of this Bestseller machine:
Then there are systems for companies that make profiles to sell them. These have speeds of 60, 80, and 120 meters per minute.
With these speeds, manual packaging of profiles is prohibitive, since the profiles come out at a rate of 40 pieces per minute.
A plant of this type is the Coil To Pack D4K system, which you can see here.
Profiles are available in the market with standard lengths, for example, 3, 4, and up to 6 meters.
These profiles, especially the studs, must be adapted on site to the actual height of the room, and it is normal to produce waste.
In the case of large projects, it is possible to produce “custom” profiles to deliver to the final customer profiles already ready to be installed.
In this way, installation is faster and there is no waste of material!
All this is possible with Coil To Pack lines: in practice, we transfer from the central network to the machine a job list.
It’s a perfect application of the Industry 4.0 concepts.
CONTACT US
Andrea Dallan
CEO – Dallan Spa