An essential factor of success: Dallan Checkpoint in-line quality control
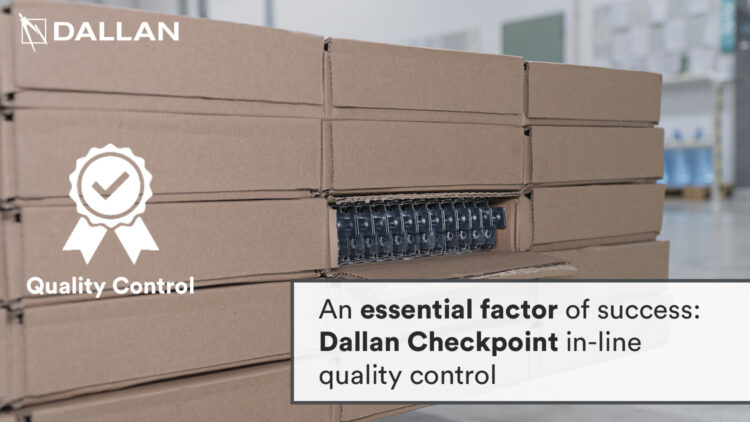
In a Dallan Coil To Box line, the operator is responsible for keeping the line supplied with steel coils, feeding the cardboard sheet warehouse, and unloading the finished pallets.
It’s unthinkable to ask them to check every profile as well!
Want to discover more?
CONTACT US
However, once packaged, it would be impossible to identify a quality issue until the box is opened, potentially thousands of miles away!
This occurred with the very first line, and for this reason, we integrated an in-line quality control system into the Coil To Box system: each profile passes through a special station where specific measurement cameras check each piece for tolerances, color tone of the capping, and alert the operator if there are deviations.
A special work cycle discards any potentially defective piece (for example, a poorly positioned hook) and if the defect repeats on more than one piece, it stops the machine safely, allowing the operator to perform checks and corrections. In this way, I ensure that every box of profiles that will be opened will contain no surprises, but only perfect profiles!
Dallan Boxing station: a tireless packaging machine
T-bar profiles, once checked one by one, arrive at the fully automatic boxing station. This station starts from a warehouse of open cardboard boxes, cut to size for each type of profile, which are placed externally on a mobile pallet on wheels.
The boxes are folded in the machine and the profiles are inserted inside in one or two layers, as is done for the Cross Ts. In this case, the machine even inserts an intermediate cardboard sheet to prevent the profiles from being damaged inside the box: once filled, the box is perfectly sealed through gluing.
This system allows packing up to 27 Main Runner profiles every minute, and over 80 Cross T profiles in the combined Dallan D58100 system!
Final palletizing, marking, and Industry 4.0
Cardboard boxes exit the lines at a rate of about one every 40 seconds: a palletizing robot organizes the boxes on the final pallet: this allows the single operator to handle the raw material loading stations (galvanized sheet, pre-painted, clips, and pre-cut cardboard sheets) and the unloading of pallets at the end of the line.
Often, a labeling station is also added in line for marking and identifying the boxes – since it’s impossible to know which profiles are inside without opening them!
The system control is also possible remotely, with the production programs sent directly from the office through the special Dallan software that can communicate with your ERP: a team of nine internal software developers at Dallan ensures the perfect integration of this system in an Industry 4.0 perspective and remote assistance in case of need.
Contact our experts to learn more!
CONTACT US
Andrea Dallan
CEO – Dallan Spa