Herstellung von Trockenbauprofilen: Das Coil-to-Pack-System
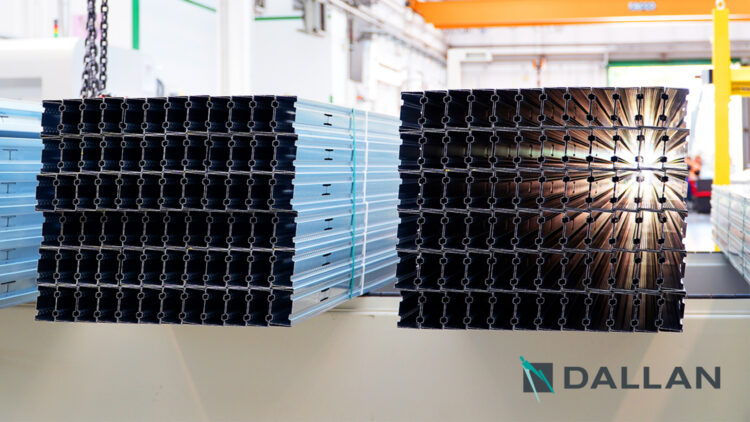
Das beeindruckendste Hochgeschwindigkeits-Produktionssystem ist mit Sicherheit das Coil-to-Pack System für Trockenbauprofile.
Diese Anlagen produzieren mit einer Geschwindigkeit von mehr als einhundert Metern pro Minute und die Besonderheit dieser Anlagen ist, dass die gefertigten Profile (in der Regel C- oder U-Profile) ein außerordentlich großes Produktvolumen am Anlagenausgang generieren.
In diesem Sektor arbeiten wir mit allen europäischen marktführenden Unternehmen zusammen und mir war es wichtig, Erfahrungsberichte von Unternehmen unterschiedlicher Größe in dieses Kapitel aufzunehmen, um zu zeigen, dass die Automatisierung für jede Art von Unternehmen in diesem Sektor enorme Vorteile mit sich bringt.
Der Markt verlangt, dass diese Profile auf unterschiedliche Art und Weise verpackt werden. In den meisten Fällen wird verlangt, dass die Profile paarweise zusammengesteckt werden (das obere um 180° gedreht) und diese Profilpaare dann zu kleinen Paketen zusammengestellt werden.
Die Pakete werden dann umreift und zu einem größeren Paket gestapelt, das ebenfalls umreift wird. Oft wird unten am großen Paket eine Holzleiste befestigt (wir nennen das Masterpack).
Bis zu den 90-er Jahren produzierten die Maschinen im Allgemeinen bis zu 60 Meter pro Minute und die Produktion konnte noch in Handarbeit weiterverarbeitet werden. Noch heute werden die Profiliermaschinen mit einer Geschwindigkeit von 60 Metern pro Minute von uns gebaut und sind nach wie vor ein Bestseller von Dallan. Oft werden sie mit halbautomatischen Verpackungsstationen kombiniert, bei denen die Profile vom Bediener von Hand zusammengestellt werden und die Maschine das automatische Verpacken des kleinen Pakets übernimmt.
Entnommen aus dem Buch „Die Revolution der Effizienz“
FORDERN SIE DAS BUCH KOSTENLOS AN
Die Firma West Hungaria Bau ist ein ungarischer Hersteller von Trockenbauprofilen. Heute laufen in der Firma zwei Profilieranlagen für Trockenbauprofile mit einer Produktionsgeschwindigkeit von 60 Metern pro Minuten und einer halbautomatischen Verpackungsstation. János Majer, Produktionsleiter der Firma, äußert sich wie folgt über Dallan:
“Die erste Maschine haben wir 2003 gekauft und mittlerweile über 54 Millionen Meter Profile damit produziert. 2019 haben wir die zweite Maschine angeschafft und wir hoffen, dass wir damit vergleichbare Leistungen erzielen können. Dallan ist ein Unternehmen mit einem starken technischen Hintergrund und großem Know-how.”
János Majer
Ab Ende der 90-er Jahre stieg die Nachfrage nach Trockenbauprofilen stark an und die Kunden suchten nach Maschinen mit immer höheren Produktionsgeschwindigkeiten.
Jahrelang haben wir Anlagen mit einer Geschwindigkeit von 80 Meter Profil pro Minute gebaut, heute erreichen unsere Maschinen eine Produktionsgeschwindigkeit von 120, 160 und 240 Meter Profil pro Minute.
Bei diesen Geschwindigkeiten war eine manuelle Handhabung der Profile nicht länger möglich. Wir haben deshalb gemeinsam mit unserem italienischen Kunden, der Firma Mangini, an der Entwicklung der ersten automatischen Verpackungsanlage für Trockenbauprofile gearbeitet.
In dieser Anlage wurden die Profile automatisch auf einer Rutsche zu einem Paket zusammengestellt, bei dem die Profile waagrecht positioniert sind und eine Schicht bilden. Später haben wir eine automatische Station für die Zusammenstellung des großen Pakets (Masterpack) installiert, in der die Umreifung des großen Pakets manuell erfolgte.
Heute erlauben die Verpackungsanlagen das horizontale und vertikale Zusammenstellen der Profile und liefern Masterpacks mit einer Grundfläche bis 1,2 Quadratmetern und einer Höhe von fast einem Meter, komplett mit automatischer Umreifung und unterer Holzleiste. Diese Pakete können direkt gelagert werden.
Für die komplette Anlage ist nur ein einziger Bediener erforderlich, der sich um das Einlegen der Coils und das Entladen der großen Pakete kümmert.
Und es gibt noch einen weiteren großen Vorteil. Bis vor kurzem konnten mit den Verpackungsanlagen für Trockenbauprofile nur Pakete mit Profilen gleicher Länge zusammengestellt werden. Es musste also für das Lager produziert werden.
Heute erlauben die automatischen Verpackungsanlagen bei laufender Anlage eine Änderung der Profillänge und haben damit den Wechsel von der Produktion für das Lager zur Auftragsfertigung ermöglicht!
So können die Profile für das Ständerwerk mit dem genauen Maß der Wandhöhe gefertigt werden, was dem Endinstallateur Zeit und Arbeitskräfte spart.
Das ist eine zusätzliche Leistung, die mit der richtigen Technologie dem Markt angeboten werden kann, ohne Auswirkungen auf die Produktivität der Anlage zu haben!
Fast zwanzig Jahre nach der ersten automatischen Verpackungsanlage hat die Firma Finish Village von Valentino Mangini, die zur Unternehmensgruppe Mangini gehört, eine neue Fertigungsanlage für Trockenbauprofile mit automatischer Verpackung in Betrieb genommen.
So äußert sich Valentino Mangini über die Zusammenarbeit mit Dallan:
“Mein Vater kennt den Ingenieur (Sergio Dallan) noch aus der Zeit, als er bei Secco arbeitete und Rollen für die Profiliermaschinen plante. Die beiden verstanden sich ausgesprochen gut, so dass es über die Jahre eine sehr enge Zusammenarbeit gab, seitdem der Ingenieur sich selbstständig gemacht hatte.
In mehr als vierzig Jahren haben wir in den verschiedenen Firmen der Gruppe Mangini fast fünfzig Anlagen von Dallan gekauft und in Betrieb genommen und ich bin mir sicher, dass ich der erste war, der eine vollautomatische Verpackungsanlage für Trockenbauprofile angefragt hat.
Das war im Jahr 2000, als wir gerade eine Firma für die Produktion von Profilen für Trockenbauwände in großen Stückzahlen gegründet hatten.
Die Firma hieß LM Profili und war ein Joint Venture zwischen der Gruppe Lafarge und der Gruppe Mangini. Angefangen haben wir mit dem Kauf von zwei Profiliermaschinen mit einer Produktionsgeschwindigkeit von 60 Metern pro Minute und 2001 habe ich die erste Verpackungsstation für das automatische Zusammenstellen der Profile in Auftrag gegeben.
Für das Zusammenstellen des großen Pakets aus den bereits zusammengestellten kleinen Paketen hatte Dallan bereits eine Lösung. Das Problem war, dass die Personalkosten bei diesem Produkttyp einen sehr hohen Anteil ausmachen, und dazu kommt noch die Schwierigkeit, Arbeitskräfte zu finden.
Natürlich machten diese ersten Prototypen zu Anfang viele Anpassungen erforderlich, aber dann konnten wir viele Jahre lang von einer der ersten vollautomatischen Anlagen profitieren, bei der sich die Aufgaben des Bedieners darauf beschränkten, die Coils einzulegen und die fertigen Pakete zu entladen. Statt der bisher erforderlichen zwei Bediener war jetzt nur noch eine einzige Person notwendig!
Die Firma wurde einige Jahre später verkauft und wir entschieden uns dafür, uns weiterhin bloß auf den Vertrieb der Profile mit unserer anderen Firma Finish Village zu konzentrieren. 2017 wurde die Entscheidung getroffen, die Produktion dieser Profile wiederaufzunehmen, und aufgrund der Erfahrungen, die wir in diesem Bereich gesammelt hatten, erwarben wir eine vollautomatische Fertigungsanlage mit einer weiterentwickelten Palettierstation und allen Verbesserungen, die in fast zwanzig Jahren an dieser Anlage erwirkt worden waren.
Mein Vater und der Ingenieur arbeiten mehr als vierzig Jahre zusammen und ich freue mich, dass ich diese Zusammenarbeit heute nach dem Generationswechsel mit Andrea weiterführen kann!!”
Valentino Mangini
Bei den moderneren Anwendungen wird durch die Kombination mehrerer Module eine Produktionsgeschwindigkeit bis 240 Meter pro Minute erreicht.
Das Video, das mit folgendem Link aufgerufen werden kann, zeigt ein Beispiel:
In diesem Fall sind zwei Profiliermaschinen mit 120 Meter pro Minute parallel installiert und übergeben die Masterpacks an eine einzige Verpackungsanlage, in der die Masterpacks verpackt und umreift werden.
Eine einzige zentrale Umreifungsmaschine bringt auch die Holzleisten unter dem großen Paket an und arbeitet schnell genug, dass sie beide Profiliermaschinen bedienen kann.
Durch die unten angebrachten Holzleisten lassen sich die großen Pakete deutlich einfacher mit einem normalen Gabelstapler bewegen und es besteht die Möglichkeit, am Ende der Anlage einen Palettierroboter zu installieren, der die Pakete stapelt und palettiert, sodass sie direkt versandfertig oder für das Lager bereit sind.
Entnommen aus dem Buch „Die Revolution der Effizienz“
FORDERN SIE DAS BUCH KOSTENLOS AN
Andrea Dallan
CEO – Dallan Spa